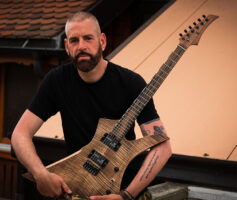
Talking Heads – Patrick Hufschmid Interview
Patrick Hufschmid is a multi-talented luthier, plectrum builder, inventor, and designer. He lives and works in Aigle, a historical town in the French-speaking part of western Switzerland, close to Montreux. Patrick literally has music in his genes – his ancestry can be traced back to composers Felix Mendelssohn and Arnold Schönberg.
Before turning his hand to luthiery, Patrick trained as a chef, before using his passion for the science of watchmaking to work as a specialised sales consultant. But Patrick never lost his love of guitars, and he trained to be a luthier before setting up his own business creating bespoke guitars and plectrums for discerning musicians.
MIN’s Andy Hughes spoke to Patrick about his background and career.
What was your inspiration to go to train as a luthier, and start your own business?
Since my teenage years, my passion for guitar has continued to grow. I started playing on an old classical guitar that I found in a bin, which my family and I attempted to restore. Afterwards, I took electric guitar lessons and began to restore and customize instruments for some of my guitarist friends. As a very curious person, I aspire to learn something new every day and I am not afraid to experiment.
Since 1996, Hufschmid Guitars has been present in the lutherie market. At the time, I had just completed my apprenticeship as a cook in Switzerland, in Montreux, before heading to Minnesota, where I joined a renowned technical school called “The Red Wing Technical College”. This training allowed me to acquire the necessary skills to repair and manufacture acoustic and electric guitars.
Where do you find inspiration for your designs?
As a luthier, I have spent 27 years experimenting with different types of woods to find the best materials for my instruments. Throughout this lengthy process, I have discovered that my preferred wood species for the neck and body of my guitars are Sapele or Sipo Mahogany, always using perfectly quartered pieces. These types of mahogany offer a unique combination of stability, beauty, and resonance that is hard to find in other woods. They also have a very bright sound, which helps to fully realize the sonic potential of the final instrument.
In addition to their tonal qualities, Sapele and Sipo Mahogany are also highly sought after for their aesthetic appeal. The wood has a beautiful grain pattern that ranges from straight to interlocked, and its reddish-brown colouring adds warmth and depth to the appearance of the guitar. Overall, I believe that the use of Sapele or Sipo Mahogany in the construction of my guitars is a key factor in achieving the high level of quality and sound that I strive for in all of my instruments.
My entire approach to guitar building is to work with well-known shapes such as the Superstrat and the Telecaster, and incorporate my own style to them. I like to improve on subtle details such as the nut material, the humbuckers, the wiring details, and the timbers I select. As Albert Einstein once said, “Everything should be made as simple as possible, but not simpler.” This quote, along with Charles Eames’ famous statement that “Details are not details, they make the design.” highlight the importance of balance in my work, between simplicity and attention to detail.
The finishes on your guitars are beautiful and highly unusual, how do you create them?
Thank you! I use natural oil varnish which I apply by hand. I build up the coats, this is a long process which can take up to two full weeks because every coat needs 24 hours to dry, then you must level it, scuff sand it and repeat the operation until the coats start to build up. I can’t stand bling and shiny finishes so I always use steel wool at the end to give my instruments a matt effect. For the stains, I use various pigments, such as brou de noix, which is a natural dye extracted from walnut bark. For example, I used brou de noix on my recent project, the Kelly inspired guitar.
You create your guitars using traditional crafts, do you believe that this makes a better instrument?
While CNC machines and other mass production techniques may be efficient, they lack the personal touch and individuality that comes with handmade craftsmanship. Each handmade instrument has its own unique character, and the process of creating it involves a level of care and attention to detail that cannot be replicated in a factory setting. The handmade approach also allows for more experimentation and creativity, which can result in new and innovative designs that may not be possible with mass production methods. Overall, handmade instruments may not necessarily be “better” than mass-produced ones, but they certainly offer a special and unique experience for both the builder and the owner.
You have been creating headless guitars since 2012. What is the advantage of that particular design for a player?
Headless guitars have been a part of the guitar world for some time now. I was first introduced to them while watching a music video by the French pop singer, Daniel Balavoine, back in the ‘80s. I have always been fascinated by their unique design, which is why I added them to my portfolio in 2012.
One of the main advantages of headless guitars is their compact size, making them an ideal option for touring musicians who are always on the go. Additionally, their lightweight construction can be a real benefit for players who suffer from back pain or strain. Another advantage is the reduced wood waste during the neck cutting process, making them an eco-friendlier option compared to other guitar designs.
Overall, headless guitars offer a more ergonomic approach to guitar building, in my case, they still retain the dimensions, weight, and shape of a standard instrument. As a guitar builder, I believe in creating instruments that don’t compromise on either aesthetics or ergonomics, and my headless guitars are a testament to that philosophy.
You use Lace Alumintone pickups. Where did you find them, what makes you use them in your designs?
The Lace Alumitone pickups that I use in my guitar designs are a perfect match for my philosophy of sleek modern design and cutting-edge technology. These pickups are a radical departure from traditional copper-based designs, utilizing aluminium instead, which results in a lower resistance and higher output, thanks to their ‘current-driven’ design.
I first came across these pickups during my research on innovative guitar components and was immediately drawn to their unique features and benefits. For instance, the exoskeleton of the pickup is water-jet cut from aluminium and paired with a micro-winding that uses 90% less fine copper wire, resulting in a low-impedance/high-impedance pickup that delivers a clear and dynamic tone. The Alumitone humbuckers are also virtually noiseless, making them an ideal option for guitarists who value clarity and reliability in their sound.
Another notable feature of these pickups is their lightweight construction, which can significantly reduce the weight of the guitar, making it easier to play for extended periods. Overall, the Lace Alumitone pickups represent a perfect blend of innovation, performance, and aesthetics, and I am proud to incorporate them into my guitar designs.
Your plectrums are beautiful works of art. Why do you think that a unique plectrum is so important.
Thank you for the compliment on my plectrums! I truly believe that the plectrum is a crucial aspect of the entire guitar playing experience. It’s the tool that you use to play the instrument, so it’s important that it feels comfortable, efficient, and inspiring in your hand.
For years, I’ve been fascinated by the idea of creating plectrums that reduce playing effort while also improving playing efficiency and strength. After experimenting with various concepts, I naturally came up with the idea of using thicker plectrums to achieve this goal.
By using thicker plectrums, guitarists can enhance their playing efficiency and strength while reducing effort. This innovation minimizes hand movements and increases hand strength, resulting in less cramps and tensions. This feature is particularly beneficial for guitarists who suffer from muscular problems such as arthritis or tendonitis. But even guitarists without these issues can benefit from this bio-mechanical phenomenon. It can help them achieve greater precision, force, and speed in their playing, making it an attractive option for adventurous musicians.
I believe that the plectrum can also be a work of art. By combining innovative designs with high-quality materials and craftsmanship, I aim to create plectrums that not only feel great in your hand but also look beautiful and unique. Ultimately, my goal is to inspire guitarists to explore new musical territories and achieve their full potential as musicians.
When you were first learning to design and manufacture guitars, what were the initial technical issues you had to overcome?
When I first started learning to design and manufacture guitars, I faced a number of technical challenges that required careful attention and problem-solving. One of the biggest issues was learning how to create a high-quality neck joint, which is a critical component of any guitar design. I spent a lot of time experimenting with different techniques and materials to find the best approach.
Another challenge was learning how to select and work with different types of wood. I had to become familiar with the properties of various woods and how to properly shape and finish them to achieve the desired results.
I had to learn how to properly install and wire pickups, which can be a complex and delicate process. This required careful attention to detail and a lot of trial and error to get it right.
Overall, the process of learning to design and manufacture guitars required a lot of patience, dedication, and perseverance. It was a steep learning curve, but it was also incredibly rewarding to see the results of my hard work and dedication come to life in the form of beautiful, high-quality instruments.
Do you have any famous customers?
While I have had the pleasure of working with some famous musicians, it’s the passionate players who truly inspire me. Knowing that my instruments are appreciated by those who value the craftsmanship and quality is what drives me to continue creating.
Who would you like to design and built a guitar for?
Honestly, I am excited to design and build a guitar for any passionate player who appreciates the craftsmanship and unique design of my instruments. Each guitar I build is a collaboration between myself and the player, and I am always eager to take on new projects and bring it to life.
Where do you source the materials for your guitars?
I source my materials from a variety of trusted suppliers and manufacturers around the world. The specific details are a closely guarded secret, but I can assure you that I only use the highest quality materials to ensure the best possible sound and performance from my guitars.
What’s your favourite part of the design and manufacturing processes?
I find every aspect of the design and manufacturing processes incredibly fulfilling, as they culminate in the creation of a remarkable guitar. There’s something truly captivating about bringing individual pieces of wood together, and watching them transform into a musical instrument that can produce such an incredible sound. It’s almost like a fourth dimension, where the physical construction in three dimensions combines with the auditory dimension to produce the final result. I’m thrilled by the various stages of the construction process and how they all contribute to the ultimate outcome.
When you started, where did you learn the business side of things – how to export your instruments, ensure you got payments through, and so on?
Prior to my work in the guitar-making industry, I gained extensive experience in the luxury goods sector as a specialist sales consultant for wrist watch complications back in 2007. The in-depth training I received on branding and the handling of high-end goods has significantly influenced my current work, especially with regards to exporting my instruments. I pride myself on being a meticulous and responsible individual, with a keen eye for detail and a methodical approach to all aspects of business operations. My previous experience has equipped me with the necessary skills to manage complex logistics and ensure seamless transactions, and I am committed to delivering the highest level of customer satisfaction through my work.
How important is social media in building your share of the bespoke guitar building business?
Social media has been an incredibly vital tool for building my share of the bespoke guitar building business, especially as an individual self-employed artisan in a country with a high cost of living like Switzerland. It has allowed me to connect with new customers from all around the world and establish a loyal following of clients who appreciate my craftsmanship and unique designs. As a small business owner, I am committed to leveraging its potential to the fullest. For instance, I regularly post daily videos of me working on various projects, as well as the final outcomes. By doing so, I can showcase the intricate details and precision that go into my work and provide a glimpse into the behind-the-scenes process of building bespoke guitars. This has been a great way to connect with my followers and foster a sense of community, while also highlighting my expertise and dedication to quality. Overall, social media has been a game-changer for my business, and I am constantly exploring new ways to optimize its benefits.
Because of the singular way you create your guitars, is there no way to expand your business, maybe outsource some aspects of manufacture, to cut down on the time it takes to create each instrument?
As a small artisanal business owner, I am committed to maintaining my individuality and upholding the values of authenticity and high quality that set my products apart from mass-produced, faceless items.
While outsourcing some aspects of manufacture could potentially cut down on the time it takes to create each instrument, I am not interested in expanding my business and becoming bigger. I believe that there will always be a demand for unique craftsmanship, and I aim to continue meeting that need in the future. By remaining true to my artisanal roots and focusing on creating bespoke guitars of exceptional quality, I can maintain the integrity of my work and ensure that each instrument is crafted with the utmost care and attention to detail. For me, the satisfaction of seeing a customer’s face light up when they play one of my guitars is far more important than any potential profits that could be gained through outsourcing or mass production.
What is your most popular model, and do you know why it is the best seller?
My most popular model is the Superstrat shaped guitar. This particular shape has gained a lot of popularity among guitar players over the years because of its versatility and unique design. It’s a shape that can fit any playing style and genre, and it’s very comfortable to play for long periods of time. The sleek design and streamlined body shape also add to its visual appeal, making it a popular choice for those looking for a modern and stylish instrument. I believe that my attention to detail, exceptional craftsmanship, and dedication to using only the highest quality materials have also contributed to the popularity of this model. I pride myself on creating bespoke guitars that not only look great but also sound and play beautifully. It’s always a great feeling to see my customers happy and satisfied with their new instrument.
How far ahead are you planning for your business, or do you prefer simply to see what happens in the future?
As a small artisan operator, my focus is on maintaining my individuality and upholding the values of authenticity and high quality that set my products apart from faceless industrial manufacturing. I believe that there will always be a demand for unique craftsmanship, and my goal is to continue meeting that need in the future. While I do have plans for expanding my brand and exploring new opportunities, I prefer to focus on the present moment and take things one step at a time. For me, the most important thing is to continue producing bespoke guitars that not only meet but exceed my customers’ expectations, and to ensure that every instrument is crafted with the utmost care and attention to detail. Ultimately, I believe that living in the present moment is the most important thing, and it’s something that I try to keep in mind as I work on each new project.
www.hufschmidguitars.com
The post Talking Heads – Patrick Hufschmid Interview appeared first on Music Instrument News.
Source: musicinstrumentnews.co.uk