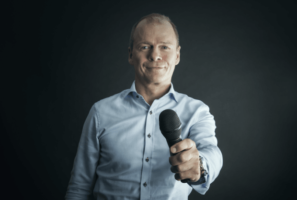
DPA on ‘pushing the boundaries of what’s possible’ in pro audio
Recognised for its appliance of science and miniature microphones, DPA has become an international brand while maintaining the image of a small Danish developer. Kevin Hilton went to see its production and R&D facilities and reports on the company’s latest developments, both technologically and commercially…
Despite the economic imperative to expand and increase production, the microphone business still manages to maintain many niche sensibilities. Among the companies that appear to have achieved this is Danish Pro Audio (DPA), which continues to be regarded as a specialised, low volume producer of high-quality products with a price tag to match.
Much of this still applies but in the last 10 years DPA has been increasing production and expanding its product range. This has in part been made possible through its acquisition by private equity fund The Riverside Company in December 2013. The greater stability and investment also allowed DPA to expand commercially in its crucial overseas sales markets. In December 2017 it bought long-term UK distributor Sound Network and in March this year reorganised its distribution chain in Germany.
Kalle Hvidt Nielsen, DPA’s chief executive since September 2016, feels these changes have altered how the company is perceived by those working within it rather than how it is seen by customers and the market in general. “When you grow as much as we have over the years, you need to develop your internal structure,” he says. “If you’ve got two engineers making new products, they can sit and discuss all the issues and challenges involved between themselves. But if you’re in multiple locations, you need a structure to manage the work, including sales, financing and marketing.”
While there has been corporate growth, Nielsen does not think DPA has moved away from its initial selling points of high quality and specialisation. “It’s very dear to our hearts to stick to our original mission and values in terms of not compromising,” he says. “For us it’s not hard to wait three months while working on a product to get an excellent result. As long as we lead the company by relying on the judgement of the specialists and those interacting with the customers, we can still be this close little company that can react to requests fairly rapidly.”
Like other current DPA executives, Nielsen has a background in acoustics and technology as well as management. He was previously CEO at both audiophile hi-fi manufacturer Bang & Olufsen and Brüel & Kjær Sound & Vibration Measurement. The Brüel & Kjær connection has long been important in the development of DPA. Founded in 1942, B&K was established to produce sound analysers to be used in the design of concert halls and other auditoria. In the late 1950s B&K started producing special microphones to work with its measuring equipment. Despite their very specific application, they were adopted by sound engineers to record classical music.
B&K responded to this new usage by developing the 4000 Series specifically for high-end recording work. In 1982 B&K released the 4006 omni-directional condenser mic, coinciding with the establishment of a dedicated pro audio division. Speaking in 1989, company co-founder Dr Per V Brüel said the 4000 Series microphones did not change from their measurement predecessors in terms of technology, only in size.
Despite the success of the 4006 and other recording microphones, financial pressures led B&K to eventually close its pro audio operation and concentrate on the core market of measurement and analysis. Two B&K employees – capsule designer Ole Brosted Sorensen, who worked on the 4006 and the cardioid 4011, and marketing executive Morten Støve – thought there was still potential in this market.
They set up DPA and established a distribution network to continue marketing the 4000 Series for recording work, which, over time, led to the development of new microphones for different applications. The 4006 continues to be part of the portfolio but has gone through some revisions; the 4006-TL reference standard model appeared in 2005, while the d:dicate 4006A was introduced as part of DPA’s d:dicate range of modular microphone systems in 2011.
Conventionally styled instrument, vocal and reporter’s microphones continue to be a part of DPA’s offering but since the mid-1990s it has become more associated with miniature mics for theatre production and TV presentation. The key product in this field was the 4060 omni lavalier model, introduced in 1996. This was followed by a boom-mounted headset version two years later, since when more small mic heads that can be hidden in clothing or on the body and used in conjunction with wireless systems have appeared.
As part of its research into how to make ever-smaller microphones but still with good quality sound, DPA began working with Danish hearing aid developer Muphone. This collaboration was taken to its logical conclusion in 2005 when Muphone merged with DPA. “We’ve been pushing the boundaries of what is possible,” says vice president of marketing Anne Berggrein, who has been with DPA for 14 years. “In the beginning we took measurement microphones and turned them into something for the professional market by adding features like phantom power.”
Since then, Berggrein adds, DPA has become known for miniaturisation and targeted very specific market areas: “Theatre professionals were asking for something that could be closer to the sound source. What we have now in the d:screet 4060 is hearing aid technology meeting pro audio. It was a big step for us because now 70 to 80 percent of what we are selling is based on miniature capsules.”
As well as lavalier mics such as the 4060 and recording models including the 4006A, DPA offers shotguns, the d:dicate 4017, the d:facto interview mic and instrument mics such as the d:dicate 4090. All these are produced at DPA’s factory in Asnæs on the Danish island of Zealand, some 90 kilometres (55 miles) west of Copenhagen. The majority of components are made here, with the notable exception of the 4006’s capsule, which continues to be bought in from B&K.
The factory, despite being a fairly non-descript industrial building, is light and airy inside. It accommodates just over 100 employees, many of whom are women working on the assembly lines and in the quality test areas. Production line manager Finn Mortensen, who is in charge of miniature capsule manufacture, comments that women have the patience to concentrate on assembling such small items, with 90 per cent of their work carried out under microscopes.
The bulk of the work is by hand, using tweezers. A welding machine is one of the few pieces of mechanised equipment involved in the process. The length of time it takes to produce a microphone varies from product to product. Mortensen estimates that mics in the d:screet miniature series, which includes the 4060, take between four and five weeks to build. “It takes three days to make the earpiece,” he says. “But it’s like making a fine wine – it takes time.”
In recent years production has been scaled up, primarily to accommodate production of the CORE amplifier, launched in October 2017. This is promoted as giving a 14dB increase in sensitivity, enabling the mics to go from “a whisper to a scream”. Kalle Hvidt Nielsen says the CORE was part of an ongoing attempt to produce ever better sound: “If the microphone is the determining factor in the audio chain, what makes a good mic? It needs to be small and extremely robust, coping with things like sweat and make-up. It also needs clarity and by updating the amplifier on the miniatures we have made significant improvements.”
The existing Legacy amplifier will continue to be produced for at least another 18 months but Nielsen says the CORE becoming popular in a short space of time came as something of a surprise. “That was the main reason for us to scale up production,” he explains. Asked whether having access to increased funding through the ownership of The Riverside Company, Nielsen replies, “With stronger financial support it’s easier to look a little longer term and maybe put some more investment into something that is good for the company.”
The deal to buy DPA from Sorensen, and Støve – neither of whom are now involved with the company – was described by The Riverside Company as “seeking add-ons”. Upscaling production can be seen as fulfilling part of that, as can the acquisition of Sound Network. The distribution company was founded by Ralph Dunlop and Pete Wandless to handle several high profile pro audio brands, including Sony and Quested Monitors, as well as DPA, which it has represented for over 21 years and helped push into the important UK theatre market.
When Dunlop and Wandless decided to retire, DPA was given the opportunity to buy the company, which it decided was the best move. “We were afraid of what would happen if someone else bought it,” comments Berggrein. Sound Network is now a subsidiary of DPA but has retained its name and continues to represent other companies. DPA has also established its own sales structure in Germany but will continue to work with former distributor Mega Audio, which takes on the role of “master dealer”.
In addition to these key European centres, DPA also has a base in Colorado, USA. This makes sense for a manufacturer that sells some 95 per cent of its products outside of its home market. The company’s headquarters are located in Alleroed, 38.8km (24 miles) from Copenhagen and house sales and marketing offices, plus R&D labs – with wind machine and reverberation room – and a demo studio.
In recent years DPA has further raised its profile with marketing initiatives including a world tour to promote its various ranges and the Masters Club, described as “a community of working sound engineers who use DPA microphones in their daily work”.
But DPA – and Kalle Hvidt Nielsen in particular – realises that all this needs to be backed up by products and technologies the customers need. “We are trying to make the perfect mic,” Nielsen concludes. “We need to do better – and I think we are doing quite well – but we need to step up innovation.”
Source: mi-pro.co.uk